The Hidden Dangers of Poor Surface Prep—and How We Fix It
Don’t Skip the Most Important Step in Floor Coating
When most people think about concrete floor coatings, they focus on the finished look—sleek surfaces, decorative chips, custom graphics, or that glossy finish that reflects light across a space. But what many don’t realize is that the true foundation of a high-performing floor lies in the surface preparation.
At Rock Solid Surfacing, we’ve learned from experience: you can have the best polyurea or polyaspartic coating on the market, but if the prep is done poorly, the floor will fail.
Let’s break down why surface prep matters so much—and what we do differently.
Why Surface Preparation Is Crucial
Concrete is porous by nature. Over time, it absorbs oil, grease, moisture, and other contaminants that interfere with coating adhesion. Additionally, concrete often has high and low spots, cracks, and imperfections that can compromise the integrity of the finished floor if not corrected.
Improper or rushed surface prep can lead to:
- Delamination: When a coating peels or bubbles due to poor bonding with the substrate.
- Uneven Finish: High and low spots cause inconsistent coating thickness, reducing durability.
- Moisture Problems: Trapped moisture leads to bubbling, blistering, and mold growth.
- Reduced Lifespan: Floors with improper prep simply don’t last as long.
In short, a floor that looks great on day one could fail in a matter of months without the right groundwork.
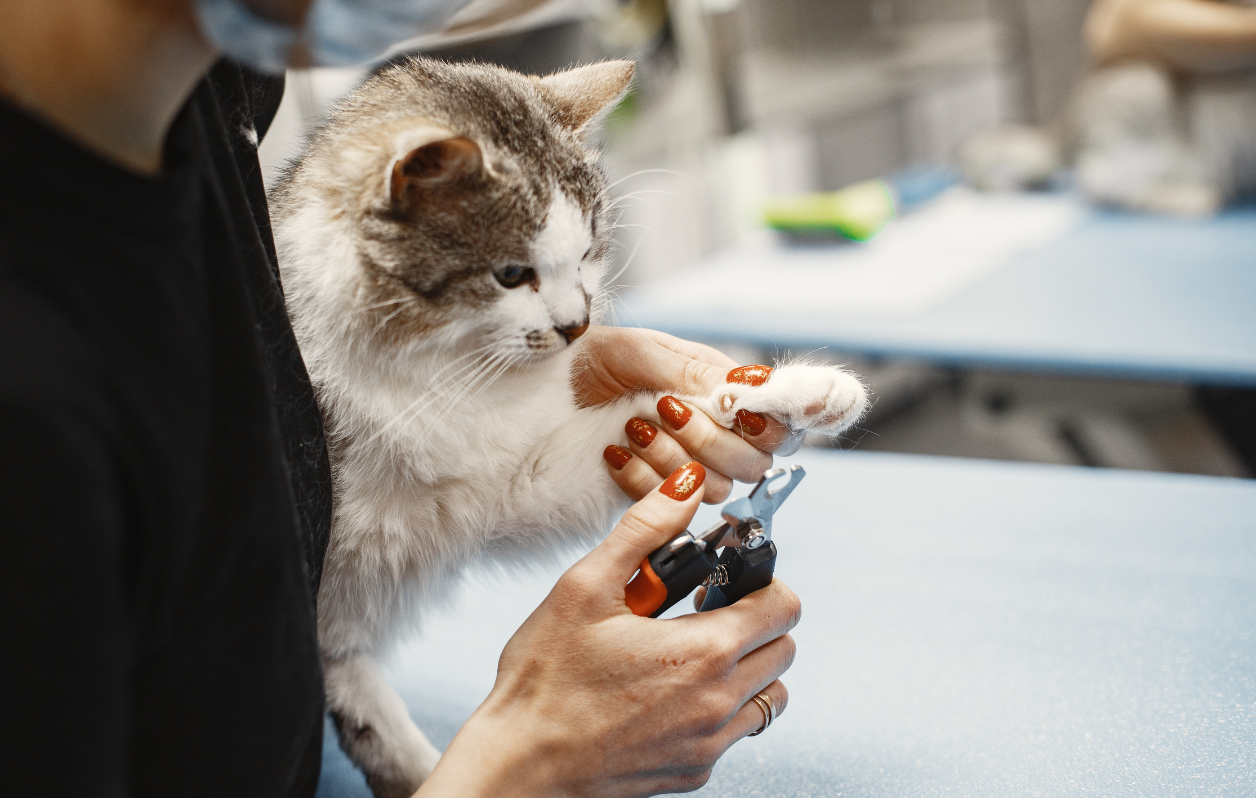
What We Do at Rock Solid Surfacing
We take surface preparation seriously. Before a single coat is applied, our team restores and prepares your concrete to be clean, flat, and ready to bond. Here’s how:
1. Crack Repair That Goes Deep
Many companies fill surface-level cracks and call it a day. At Rock Solid Surfacing, we fill cracks all the way to the bottom, typically four inches deep. We use our proprietary polyurea filler, which is absorbed into the walls of the crack and activated by moisture, curing from within and preventing pressure buildup that leads to delamination.
2. Concrete Grinding (Not Shot Blasting)
We grind every floor with high-performance, dustless equipment. Grinding removes high spots, opens up air pockets, and creates a smooth, level surface that allows our coatings to “wet” into the concrete, becoming part of the slab—not just sitting on top.
3. Moisture Mitigation
By opening up the pores of the concrete and filling all cracks, we’re able to cap off
moisture vapor, which is a common cause of coating failure in untreated concrete. The result is a dry, breathable floor that resists mold, bacteria, and humidity.
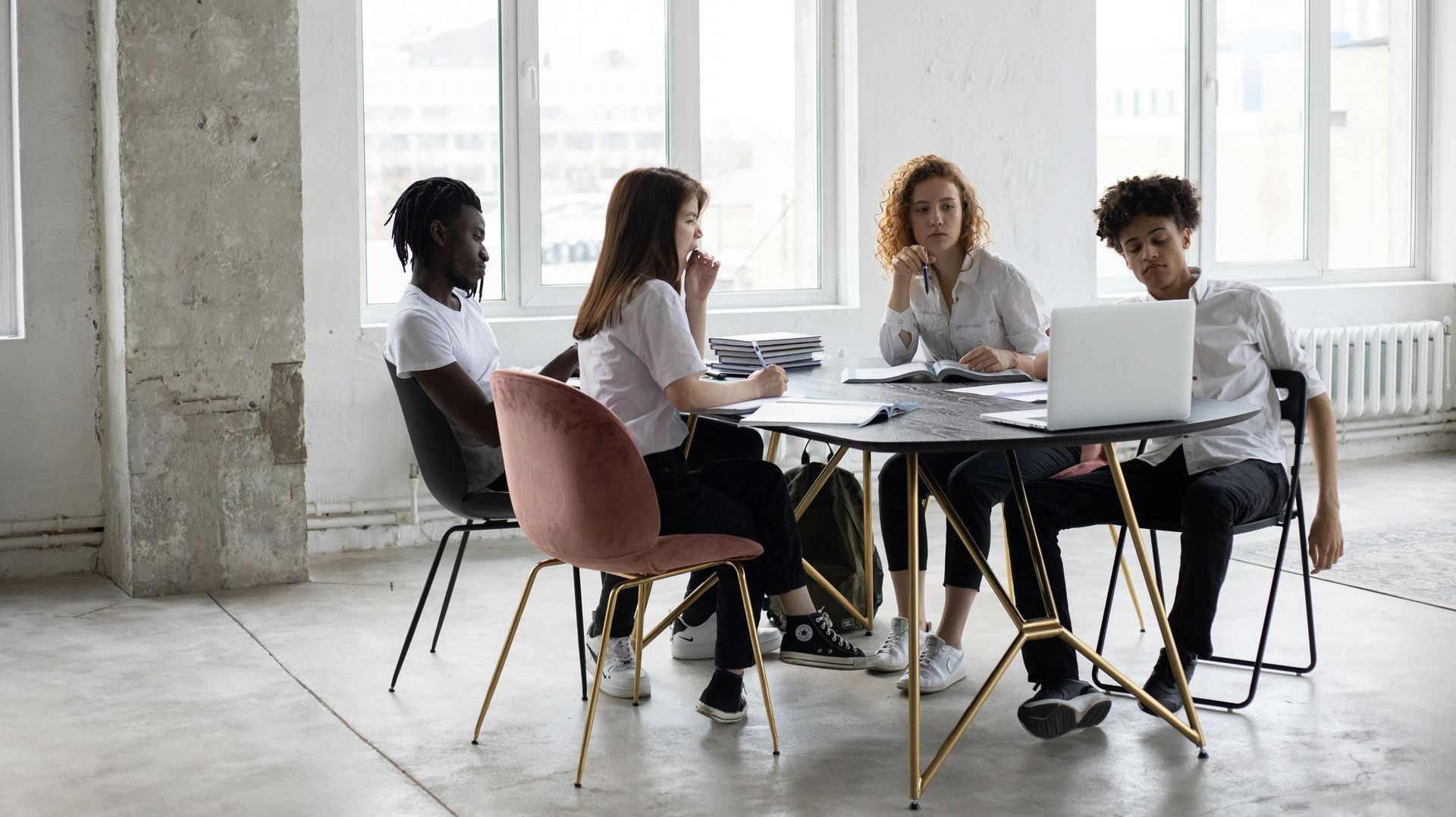
4. Attention to Detail
From cove molding to expansion joints, we make sure every edge, drain, and transition point is properly prepped and protected. This is particularly important in garages, kitchens, medical facilities, and dog kennels where hygiene and durability matter most.
Why It Matters for You
Whether you’re coating a residential garage, a commercial kitchen, or an industrial warehouse, you want your floor to last. Investing in professional surface prep up front:
- Extends the life of your coating
- Ensures a uniform, attractive finish
- Reduces future maintenance and repair costs
- Protects against water damage, cracking, and bacteria growth
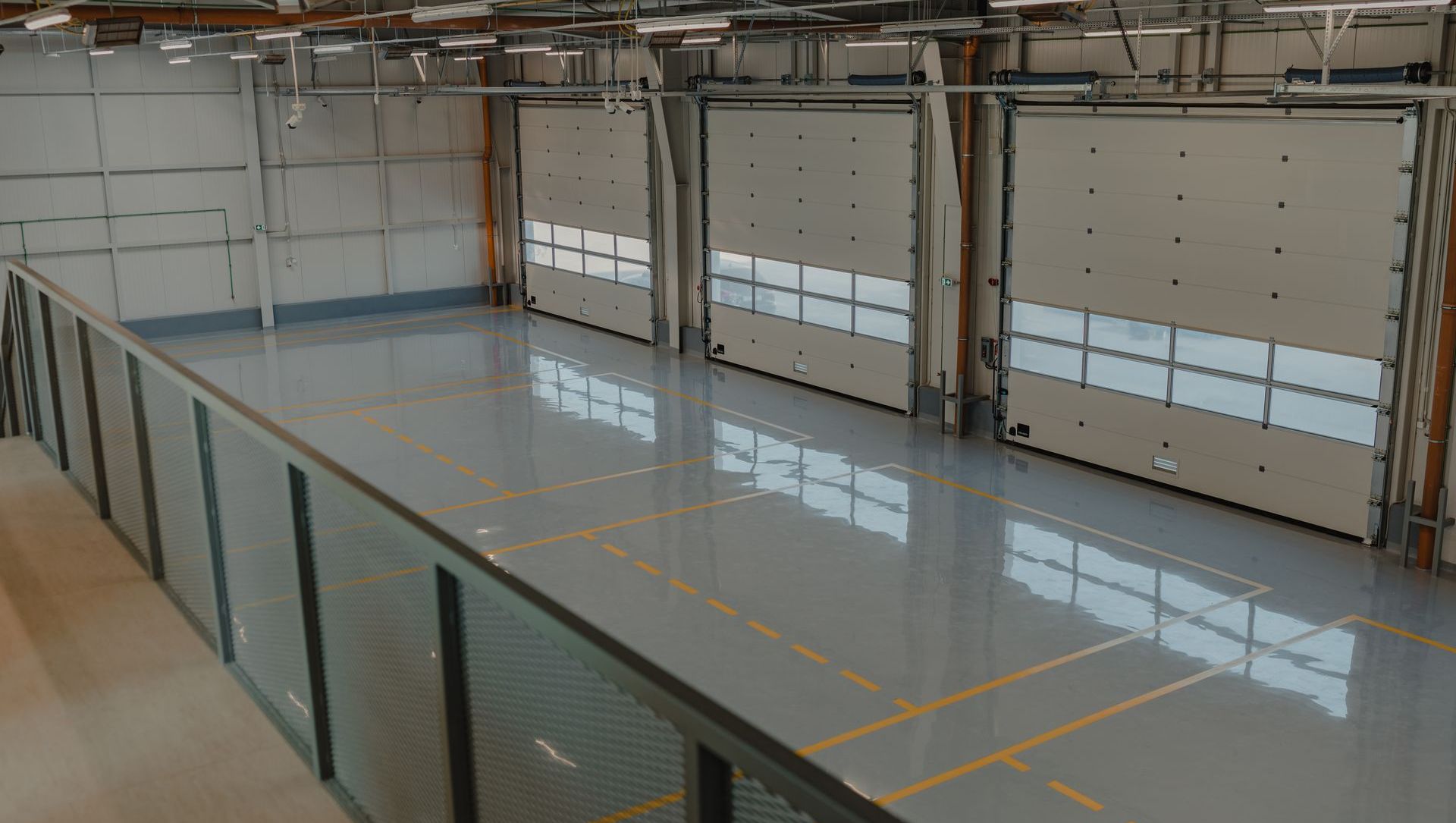
Trust the Pros at Rock Solid Surfacing
Our polyaspartic/polyurea coating system is second to none—but what truly sets us apart is our preparation process. We don’t cut corners. We fix what’s broken, smooth what’s uneven, and protect what matters most.
If you’re ready to invest in a concrete floor coating that will last for years and perform under pressure, start with a team that treats every project like it’s their own.
Contact Rock Solid Surfacing today to learn more about our process or request a quote. Your floor deserves a solid foundation—let us build it.
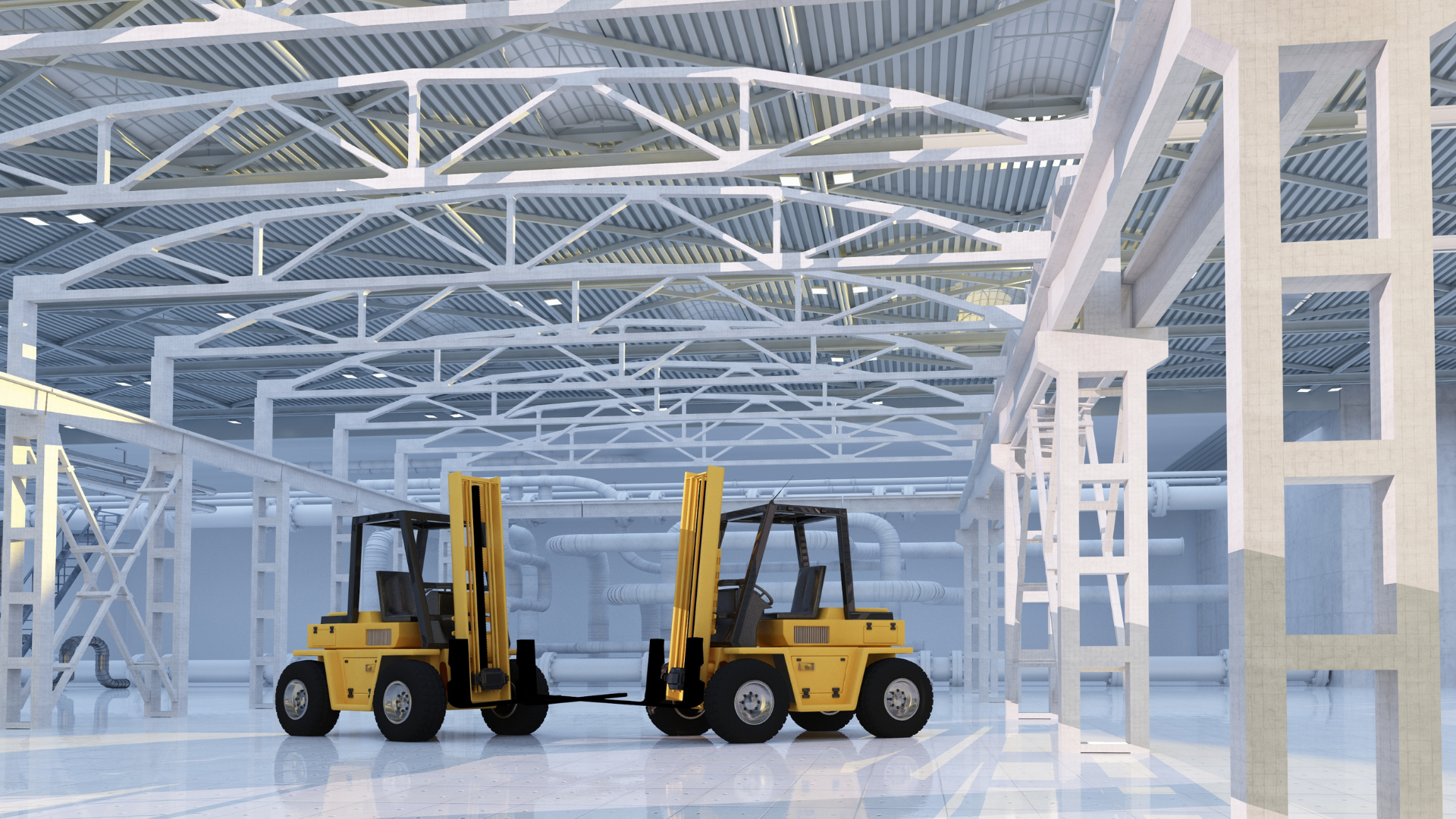
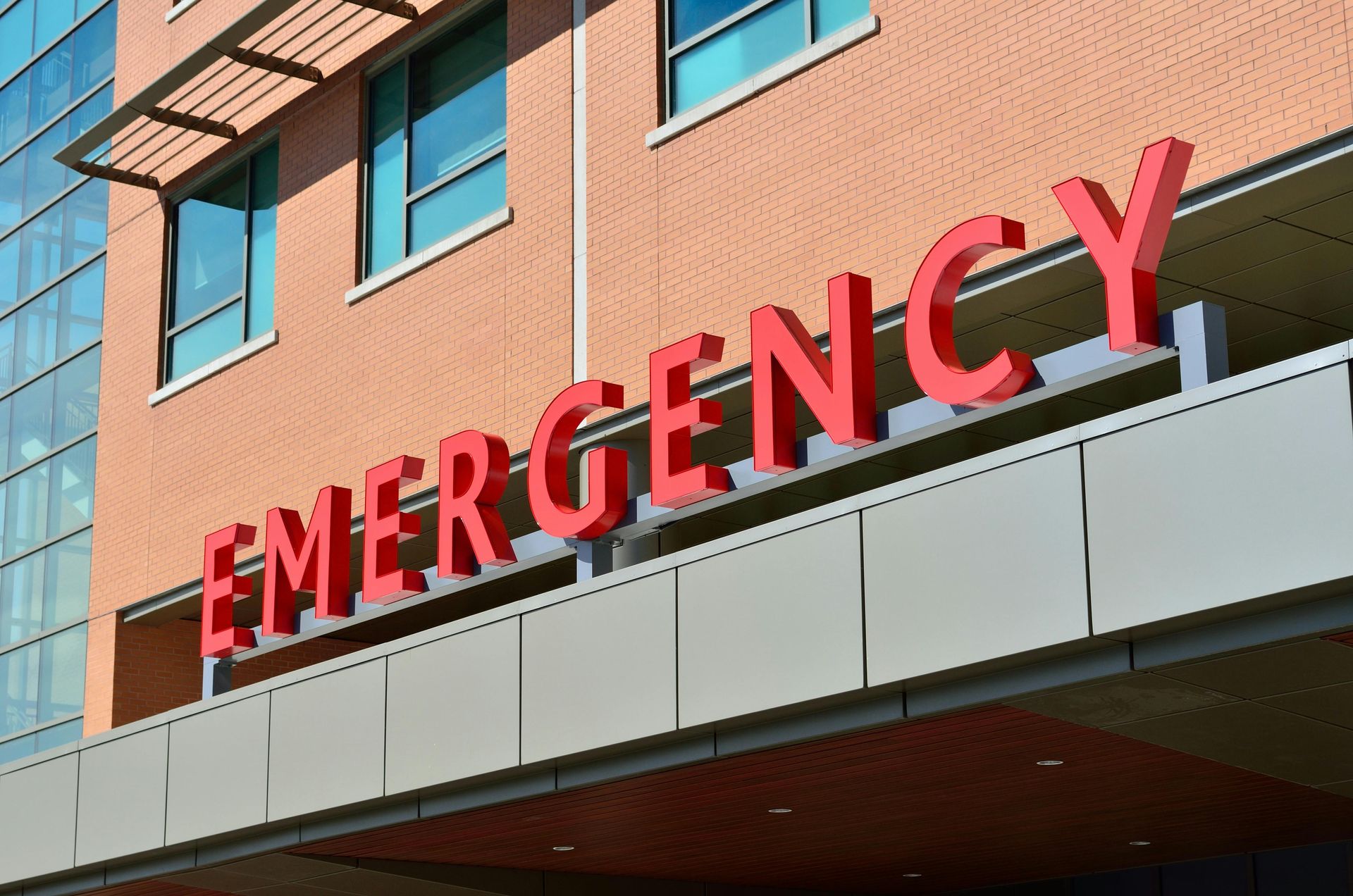
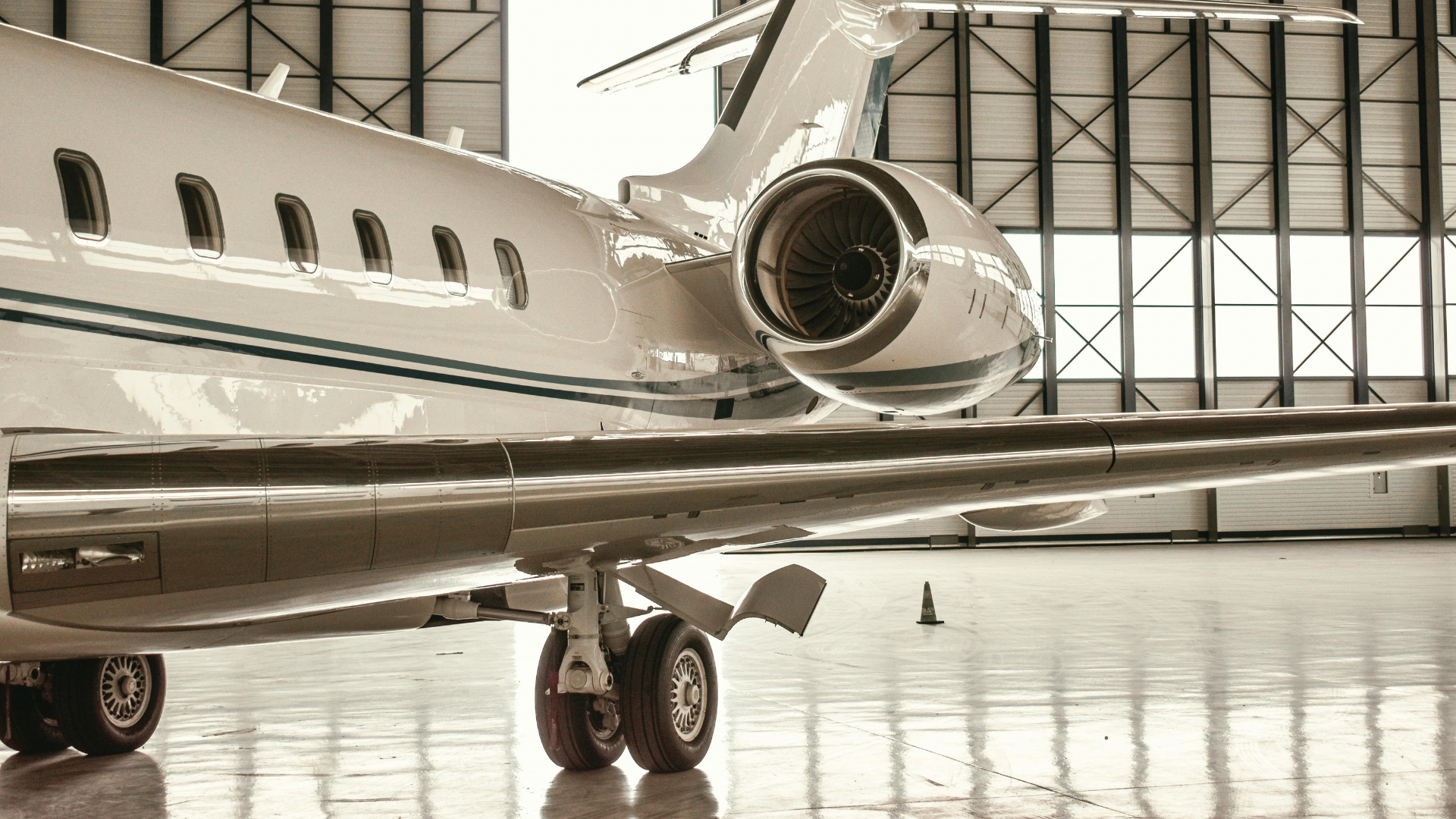
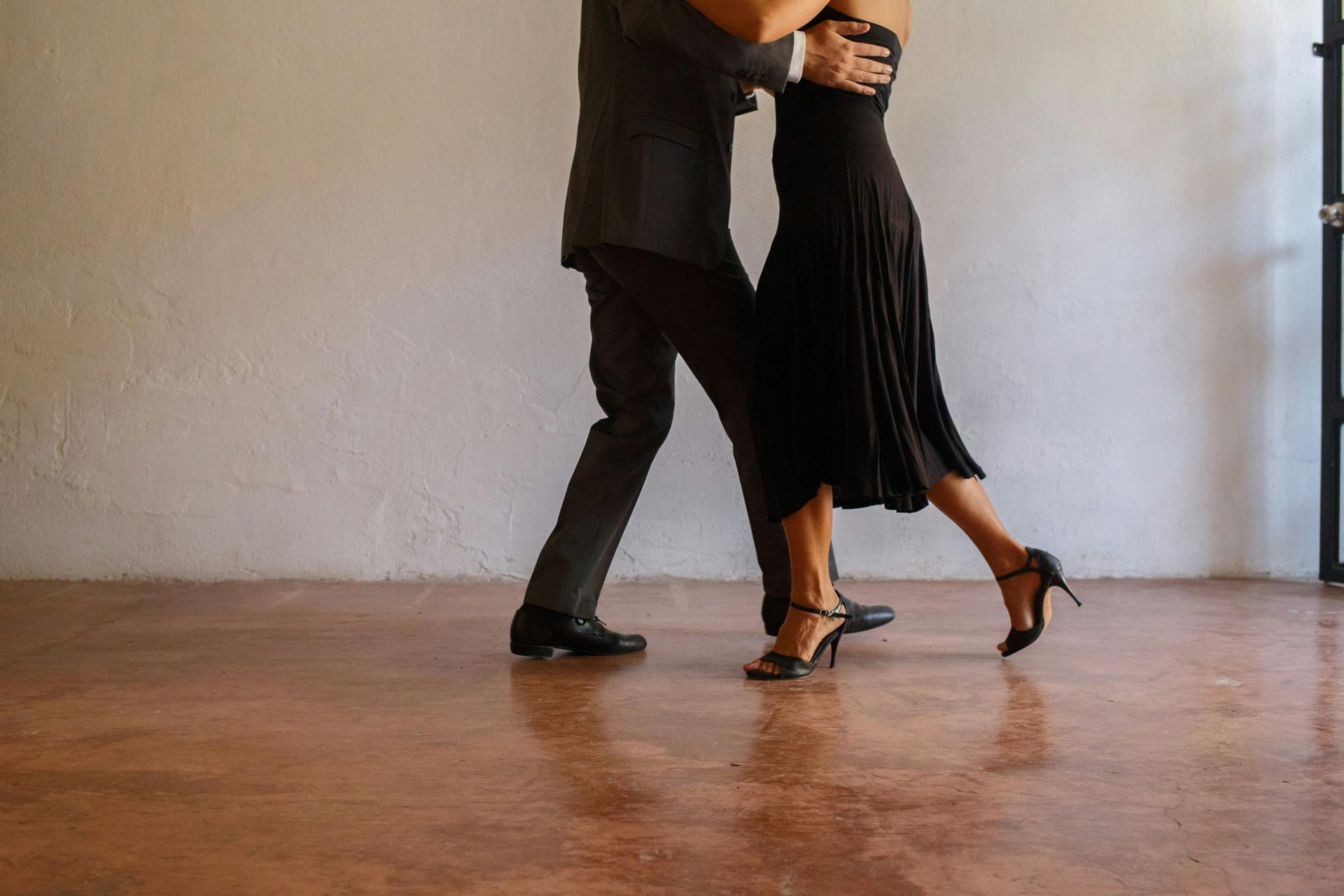
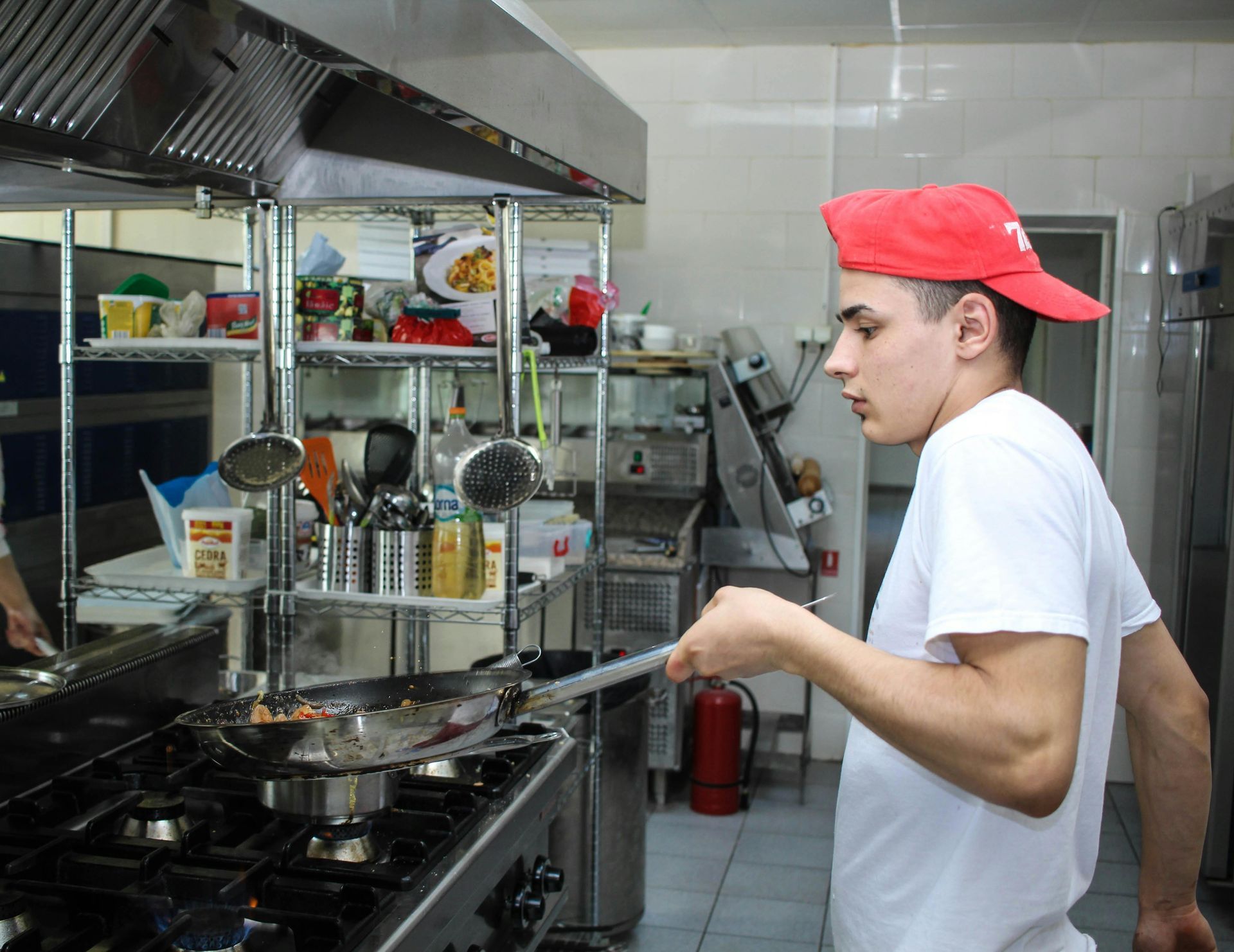
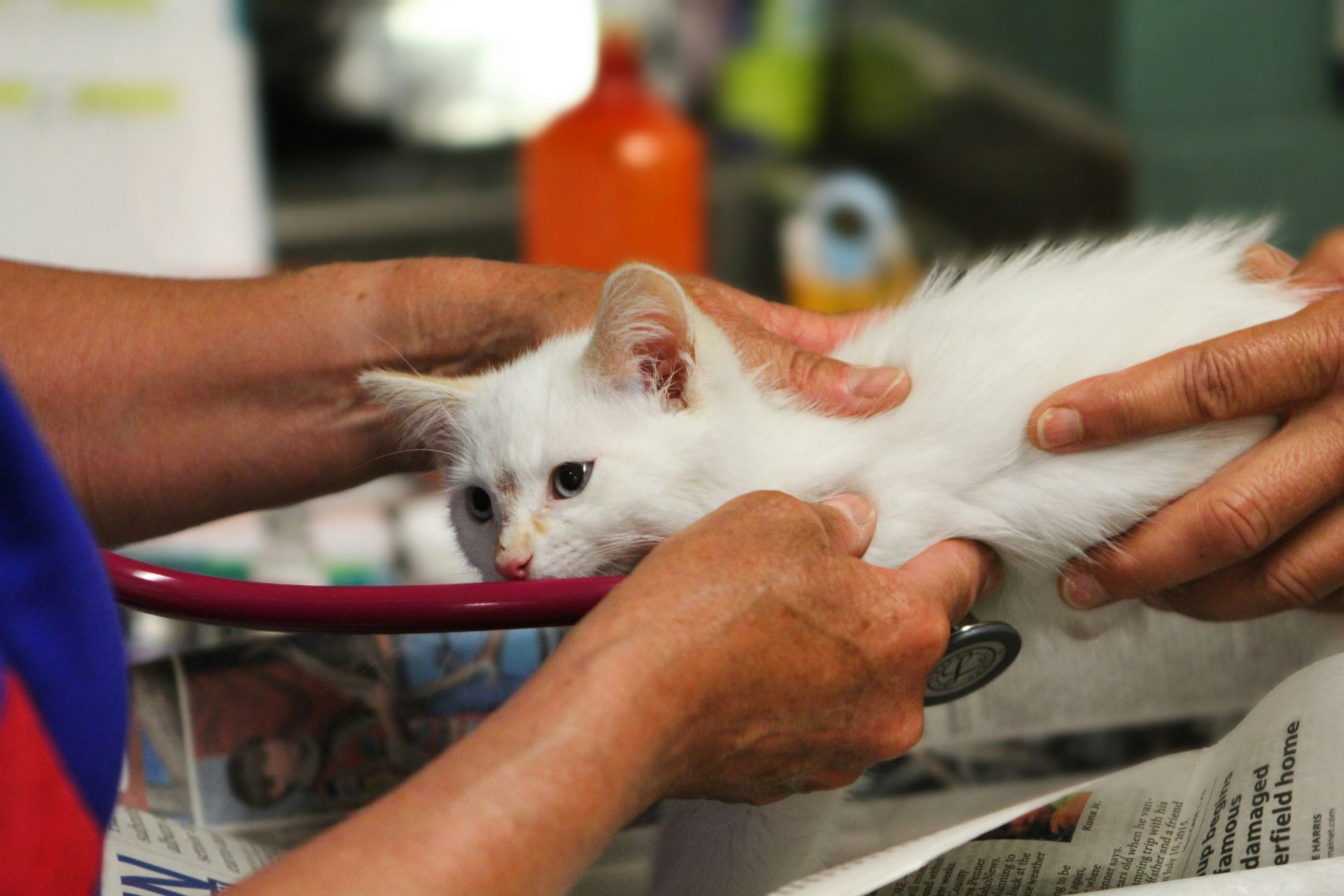
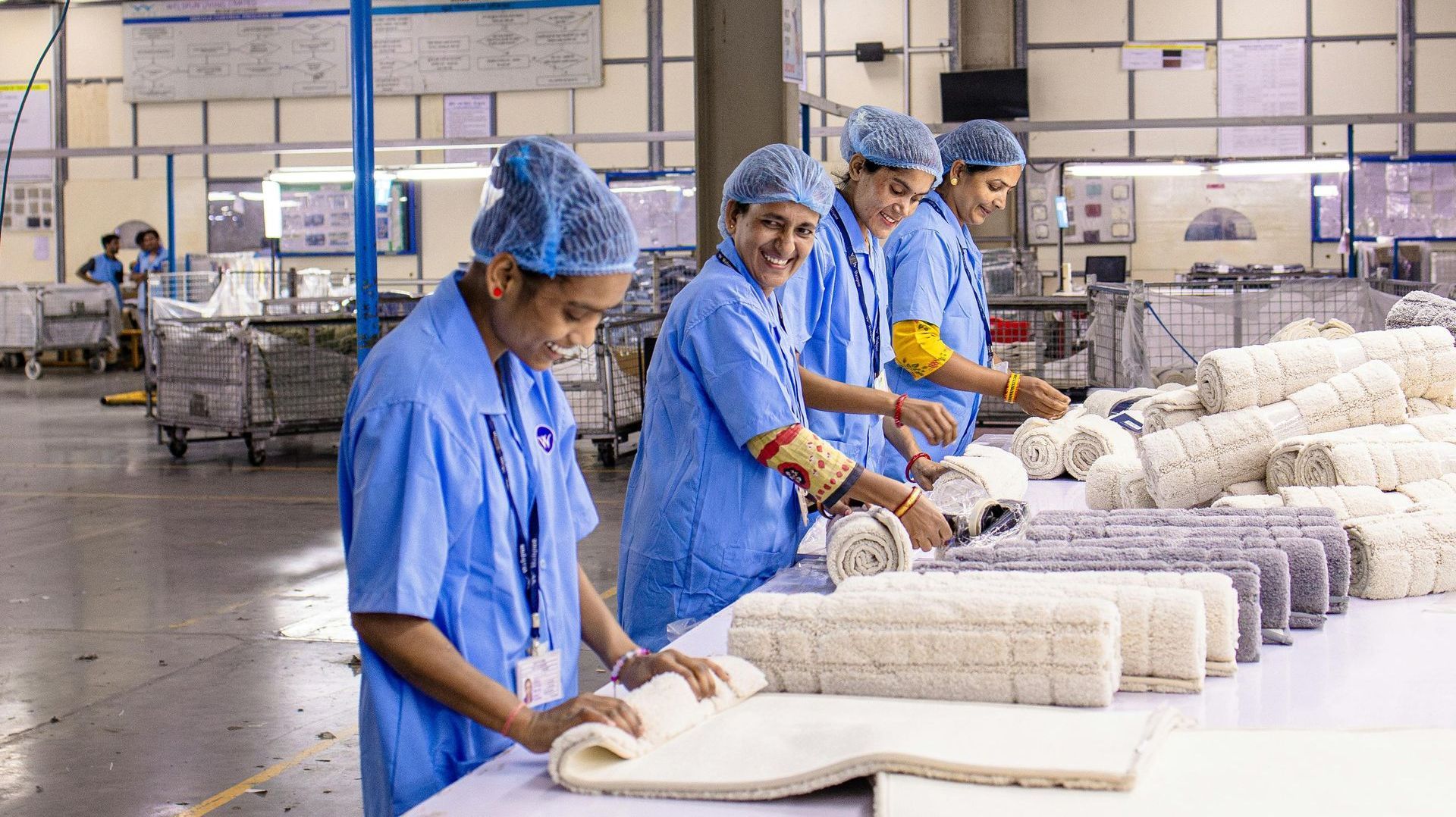
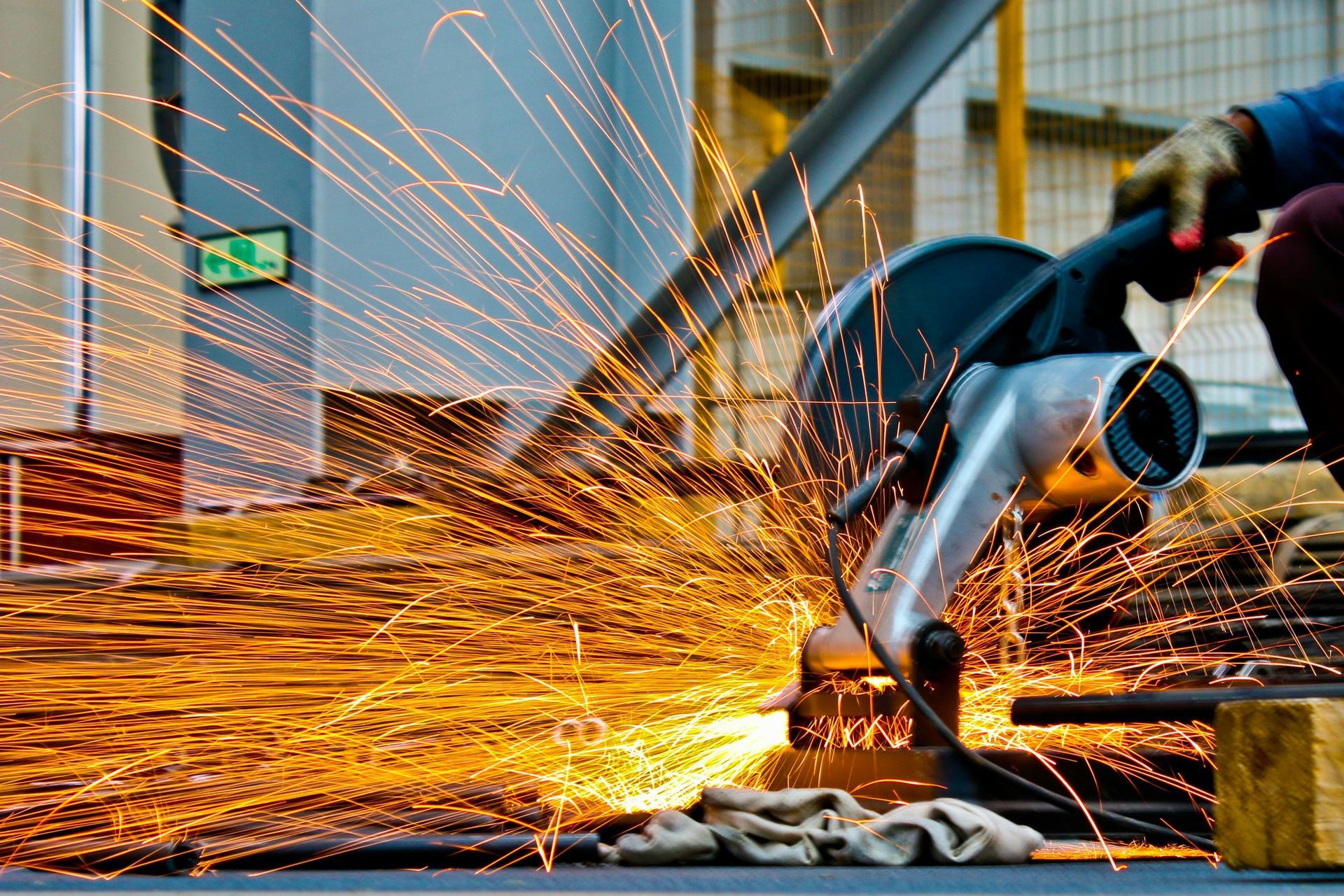
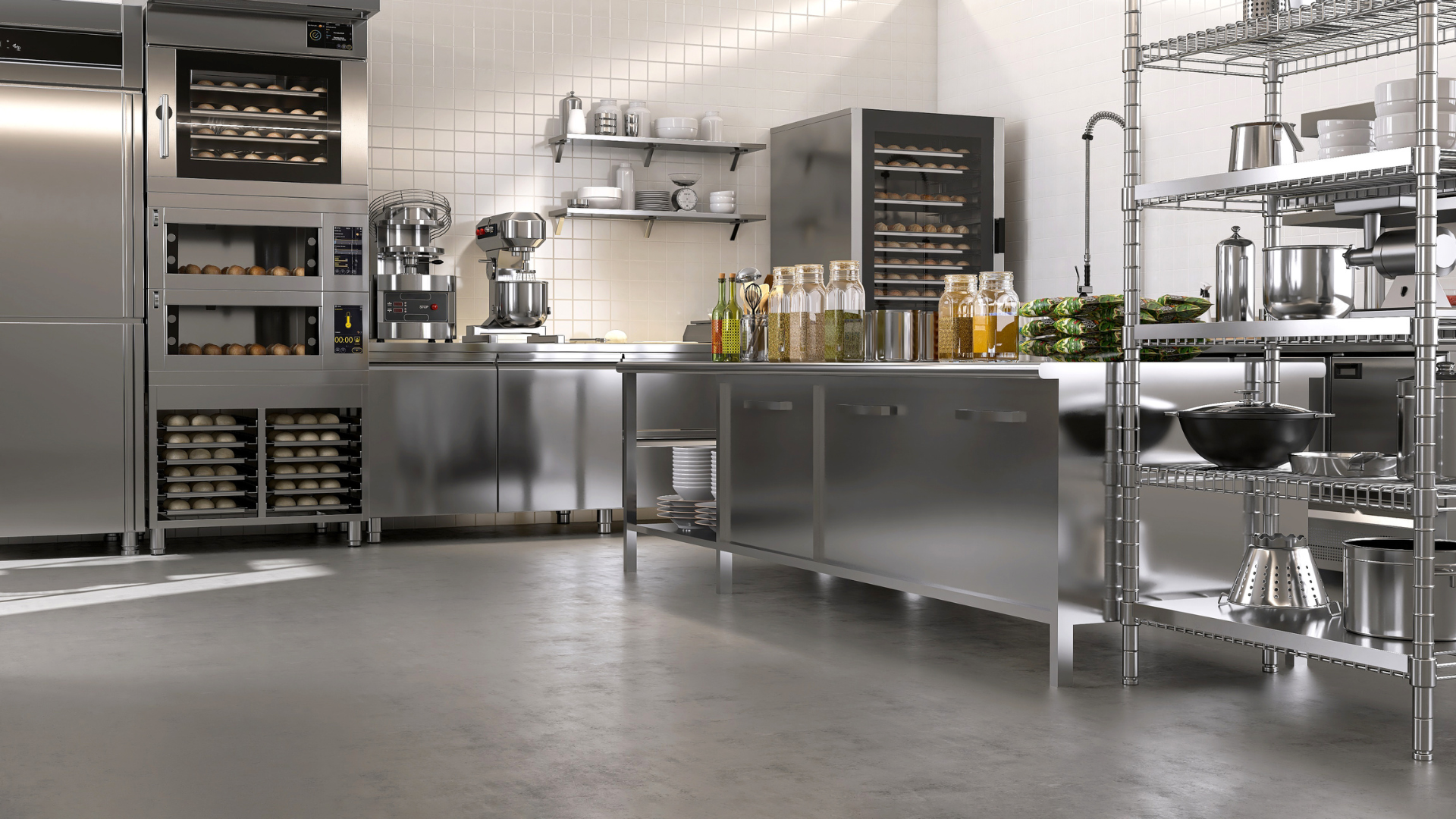
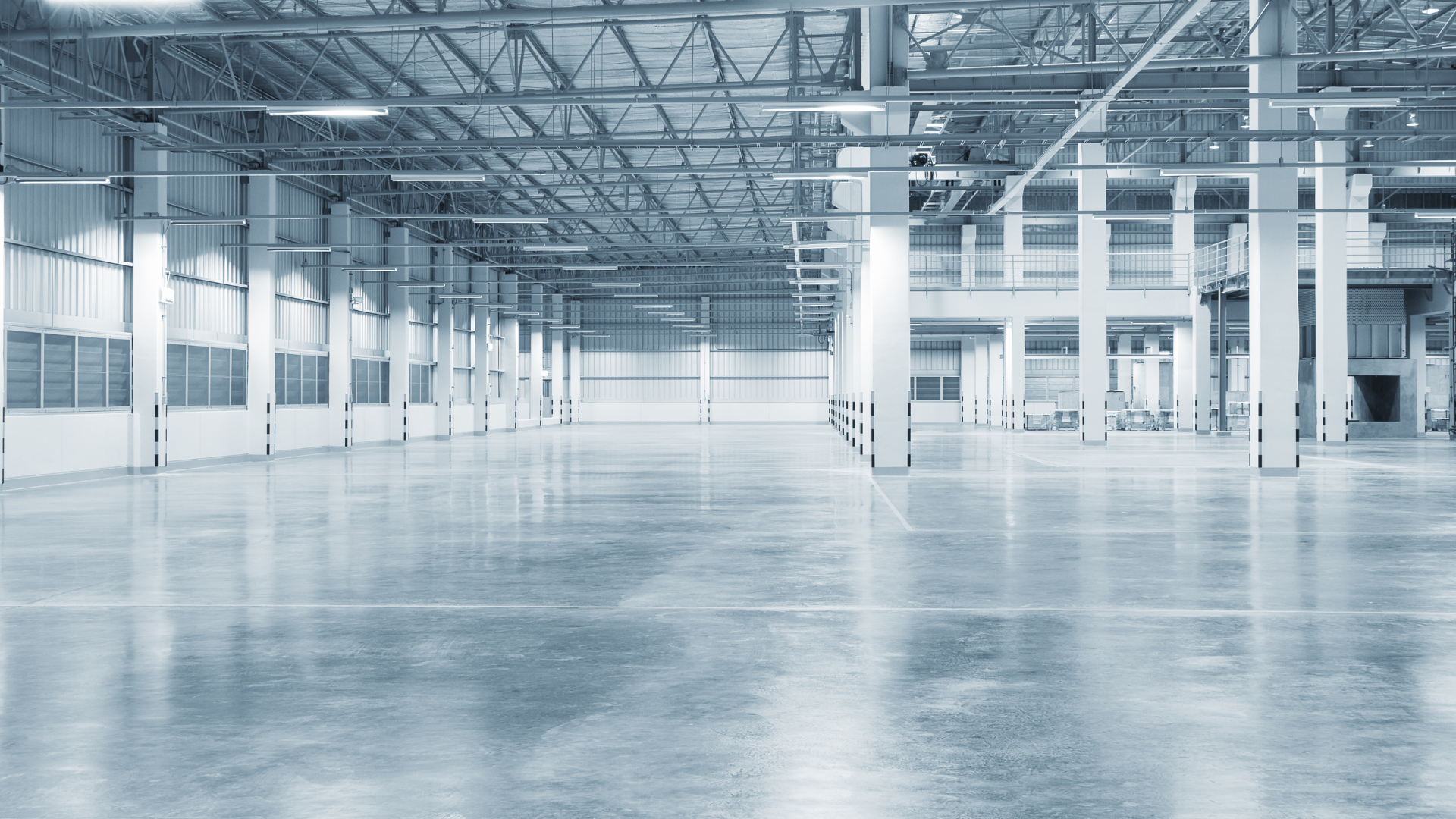